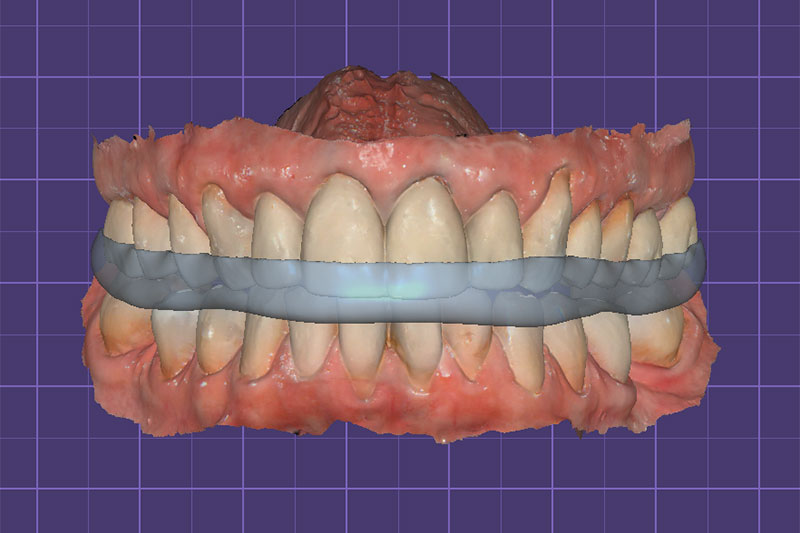
Digital Workflow For Fabrication Of An Occlusal Device


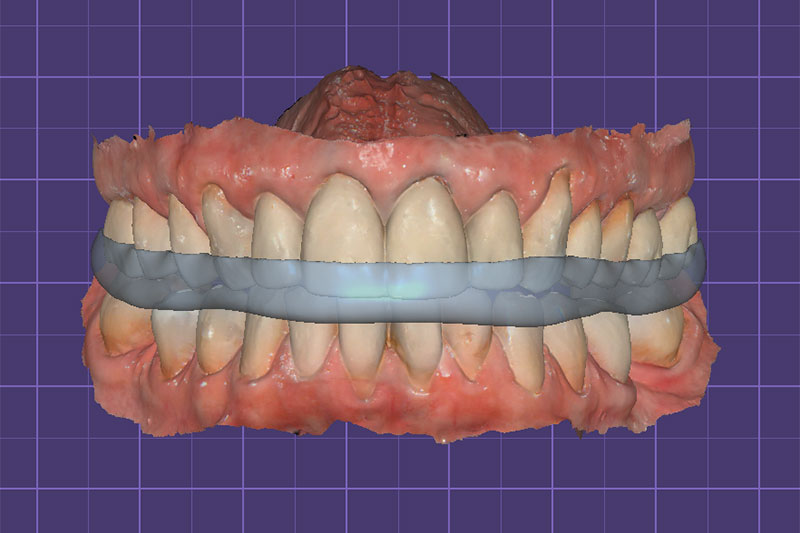
The Glossary of Prosthodontics Terms currently in the ninth edition (GPT-9), defines an occlusal device as follows:
“occlusal device \a-klo_o_ ́zal, -sal dĭ-v_ıs ́\: any removable artificial occlusal surface affecting the relationship of the mandible to the maxillae used for diagnosis or therapy; uses of this device may include, but are not limited to, occlusal stabilization for treatment of temporomandibular disorders, diagnostic overlay prior to extensive intervention, radiation therapy, occlusal positioning, and prevention of wear of the dentition or damage to brittle restorative materials such as dental porcelain; comp, bite guard, DEVICE, guard, MOUTH GUARD, occlusal appliance, OCCLUSAL SPLINT, ORTHOTIC DEVICE, STENT, SURGICAL SPLINT”
In this issue of Prosthodontic Connections I want to share with you a predictable method of fabrication of an occlusal device via either additive manufacturing (3D-Printing) or subtractive manufacturing (CNC Milling). We will review the methods of data collection necessary in the clinical setting as well as the design and manufacture of these devices in the laboratory.
At NOVA Prosthodontics we complete both the clinical and laboratory phases in the office, but you may choose to outsource the laboratory phase to your preferred commercial dental laboratory.
There are three main steps in most dental laboratory workflows. These are acquisition, design, and fabrication. These steps may occur in a purely “digital” workflow, a purely “analog” workflow, or a combination of digital and analog to achieve the desired outcome. You may be thinking that because you don’t have an intraoral scanner in your office that this means you are in a purely “analog” workflow. This is probably not the case at all. While it might remain “analog” with a traditional impression in your office, it is likely that when your impression or gypsum model reaches the laboratory it is then scanned there and the process becomes digital in the laboratory after it leaves your office.
Acquisition
A traditional impression of the dentition with an impression tray and irreversible hydrocolloid (alginate) or vinylpolysiloxane (VPS) is an acceptable method of data acquisition and these impressions can be poured with various gypsum products to yield a traditional
diagnostic cast. The gypsum casts can then be scanned in a laboratory scanner (Fig 1.and Fig 2.) to yield the digital data to be imported into the design software. A direct dental surface scan (CDT Code D0801) also commonly referred to as an “intraoral scan” or “digital impression”, has become more common in many dental offices. The intraoral scan is an acceptable method of data acquisition and may be more comfortable for the patient. This has
become the preferred method of data acquisition for many procedures at NOVA Prosthodontics. Our operatories have mounted monitors at the head and feet of the patient with mirror images allowing for easy visualization when facing either direction during the scanning operation. (Fig 3. and Fig 4.)

^ Fig.1

^ Fig.2

^ Fig.3

^ Fig.4
Maxillomandibular Relationship
The maxillomandibular relationship is a critical step in the data acquisition process that is often overlooked or the importance minimized. Failure to make this record at the planned occlusal- vertical dimension of the prosthesis, or in this case occlusal device, will surely result in an “arc of closure error”. Making this record at maximum intercuspation or centric occlusion, and then
asking the laboratory to increase the occlusal vertical dimension by “raising the incisal guide pin” on a physical or digital articulator to obtain the required restorative space in lieu of recording this space clinically will result in this error. This will make for more chair time to adjust the occlusion at time of delivery and is completely avoidable. I like to use a leaf-gauge with just enough leaves to allow for the planned thickness of the occlusal device. This is typically around 2-3 mm for most patients at the molar positions. (Fig 5. and Fig 6.)

^ Fig.5

^ Fig.6
Saving and Exporting Data
You need to save your data in a file format suitable for the software you (or your laboratory) plan to use to design your occlusal device. Common file formats are .stl, .obj, and .ply, but there are others. We use both .stl and .ply in our office for most things. The most noticeable difference visually is that .ply will be in “color” with a “wrap of photographic image”(Fig 7.) and .stl will typically be in a monochromatic view with no information regarding color or texture. (Fig 8.) Depending on your acquisition software you may need to export to one of these file formats before importing to your design software or sending to an off-site laboratory. It is a good idea to retain this data as part of the patient record as you would diagnostic casts, radiographs, photos, etc.

^ Fig.7

^ Fig.8
Design
After importing the files into your design software you can design the occlusal device to meet the specifications of the prescribing dentist. You can control and visualize occlusal contacts as well as use the digital articulator to simulate mandibular movements.



Additive or Subtractive Manufacturing
The occlusal device can be fabricated by additive or subtractive manufacturing. Additive manufacturing (3D-printing) or subtractive manufacturing (CNC milling) both yield excellent results. Your choice of material will likely dictate the manufacturing method.
Polymethylmethacrylate acrylic (PMMA) devices can be obtained using milling, but most additive manufacturing systems are limited to photo-polymerized resins. As with most materials in dentistry, they each have properties that are unique and should be selected based on the needs of your individual patient.




Delivery
If you have accurately captured the data in the acquisition and maxillomandibular relationship phase, designed your device with the appropriate retention, and with excessive undercuts blocked-out, your adjustments at time of delivery should be minimal. I hope you found this brief discussion helpful for your practice. If this is something you want to know more about or incorporate into your practice, I am more than happy to help you with this workflow. Maybe you may want to do the entire workflow in your office.
Maybe you want to do part of the workflow, or maybe you just want to make alginate impressions and the maxillomandibular relationship record. Wherever you are in your current state of practice equipment I am sure I can help you make this a reality if this is something you have an interest in for your practice. Give me a call or send us an email and we can schedule a time to talk about it. I look forward to continuing to serve the area as your prosthodontist in any way I can assist you with your practice.
Comments closed
No comments. Leave first!